Empirical design & permits
What is Empirical Design
Empirical building design refers to that part of the building code which addresses tried and proven methods of building with concrete blocks, concrete and bricks for home construction. Most building codes recognize these decades old building methods as accepted in lieu of specific design engineering plan requirements. The only requirement is that your project meet minimum empirical design criteria as specified by the code. The “Dry Stacked Construction Handbook” has an entire Chapter devoted to this topic.
This is very good news if you want to design in dry stacked block construction. As long as your building complies with these minimal requirements, then expensive engineering studies will not typically be required for building permit approval. This greatly reduces plan drawing requirements for the building code office.
The picture below shows the forms and preparation for the final concrete pour. The book provides great detail as to what has to be done before this concrete pour.
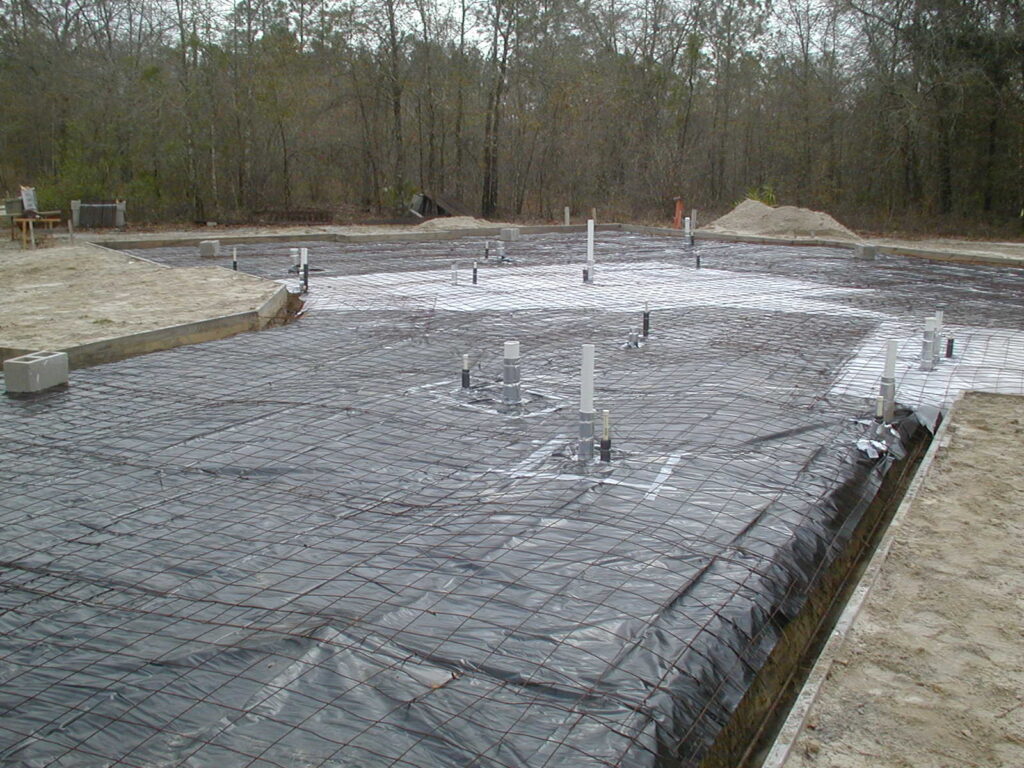
Terminology
Understanding the industry terminology is a must to expedite code research. I will point out a few of these terms in this section. When searching for these code items, look in the masonry chapters of your code for concrete block reinforcement requirements. Below is an example of one of the many home construction block data tables that can be found in code books. I have added explanation comments at the bottom of the table.
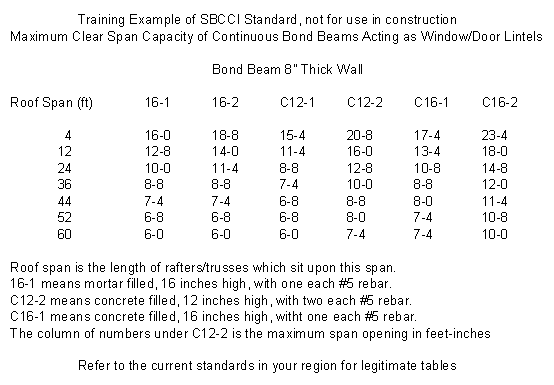
Some of the terms you will be looking for are continuous bond beam span openings, bond beams combined with lintels, vertical wall reinforcement, shear walls, and roof framing connection to bond-beam or bolted top plate.
You will have to find out what the minimal requirements are in your region, but the Florida requirements for 100-mph winds are discussed below as a representative example. Even if you are in Florida, you must still contact your permit office to see what building code is in current use, since the code changes from time to time.
Example Empirical Requirements
Examples of empirical design requirements for dry stacked CMU, are condensed into lay man terms are listed below. These requirements are representative only and must be confirmed by your local permit office.
One and two family home construction in areas with a basic wind speed of 100-mph or less, shall comply with the following:
a. Exterior walls shall be not less than 8″ thick for a multi-floor structure, nor less than 6″ thick for a single floor structure.
b. A reinforced bond-beam shall be placed around the perimeter at the top and bottom of each multi-floor wall with at least one #5 bar. A number 5 rebar refers to a rebar diameter of 5/8-inch. A number 4 rebar refers to a diameter of 4/8-inch, etc. For the first floor of a dry stacked structure, the (foundation/monolithic slab) attachment meets the bottom wall reinforcement requirement.
c. Wall area cannot exceed 240-sq. ft. without approved vertical and horizontal support, simply an in-crop or out-crop. If your walls are 8-feet high, then the maximum wall length without a corner or outcrop is 30-feet. If your wall is 9 feet high, then the maximum wall section length is about 26-feet. If your wall height is 10-feet, then the maximum wall section length is 24-feet.
d. #5 rebar reinforced wall cell grouted with concrete at each corner.
General Block Construction Requirements
The above list is the minimums to be considered for Empirical design rules. There are additional requirements specified under concrete block construction aspects of the code which consists of but are not limited to.
a. #5 rebar reinforced grouted wall cell on each side of all doors and windows.
b. Two #5 rebar in the bond beam (to meet combined lintel/bond beam requirements).
c. Two #5 rebar in all foundation footers
d. Header rebar requirements are specified in header tables within the code.
Once again, check your local code for exact requirements. For example, you may not need 2 each #5 rebars in the entire bond beam, but I did it anyway for added strength. My window and door headers were much taller than required (about 24″) but that solved many forming issues and window/door framing issues by making the headers higher than required. The code is only the minimums. You can build beyond the code requirements when you feel the need to do so.
There are also general rules relating to a ratio called the Maximum Span to Width Ratio of Floor and Roof Diaphragms. This simply means the length to width ratio of the floor plan and roof plan. For a wood stick structure this ratio is limited to 2:1, but a block structure can be 5:1. This means that if your floor plan is 40-feet deep, then it could be up to 200-feet wide (5:1 ratio). Of course, you still have the 240-sq. ft. rule to contend with, so a wall this long would need outcroppings or lateral reinforcement to break it into smaller sections for stronger home construction.
Lateral Wall Reinforcement
Typical lateral wall reinforcement refers to shear walls or some other engineered reinforcement method. Shear walls are perpendicular to the lateral forces, and work just like an outcrop. They brace the wall just like a 90-degree corner braces the wall. In other chapters I mention an inside load bearing wall. This could also be a shear wall, and could be used to exceed the 240-sq. ft. rule.
As you can see, complying with Empirical design rules is relatively easy with most home designs. Just keep these issues in mind as you plan your home design. This pretty much sums up your requirements to build under the Empirical design rules. As stated earlier, check with your permit office to confirm their current requirements.