Dry Stacked Block Construction Block Types
Preferred Concrete Block Type… two-cell blocks are preferred for several reasons. They have blunt ends unlike the three-cell blocks. This is necessary when the end of the block forms a corner. Another reason for using two-cell block type is that you can always make what I call an extended half-block when you run out of normal concrete half-blocks. These extended half-blocks can be used for door and window headers when you don’t have enough half-blocks. The final reason for using two-cell blocks is because each cell is larger which allows more poured concrete around the required rebar. Just to be clear, not all block cells are filled. Only the cells adjacent to a door or window need rebar and that cell filled. A long wall segment must have a filled cell every 8-feet.
Shown below is an example of the versatility of two-cell concrete blocks and in particular the two-cell inspection concrete blocks. Inspection blocks are required in the first row so that the inspector can see that the associated vertical wall cell rebar is properly wired to the rebar sticking out of the monolithic slab. This inspection must be conducted before blocking off the inspection port and filling the cell with concrete.
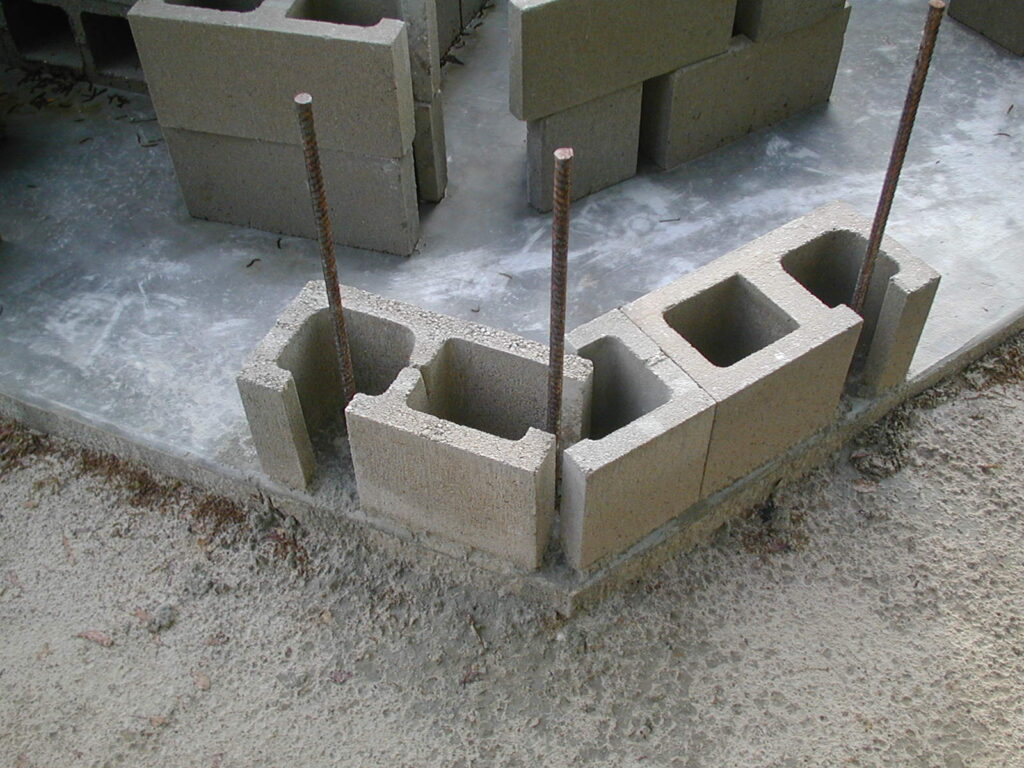
You will also need lintel blocks for the top row of blocks which form the bond-beam. Much more detail about the bond-beam is described on it’s own webpage listed in the drop-down menus.
ICF Foam Block Myths
Many ICF foam block promoters would have you believe… that Concrete Masonry Block Units (CMU) for home construction are a thing of the past. But their new deal (foam etc. blocks) may be lacking:
1. Thermal mass – CMU limits night temperature plunge in winter and daily temperature rise in summer, saving you energy.
2. Wall strength – CMU sandwiched on each side with Surface Bonding Cement (SBC) which is fiber-reinforced concrete cement, will dramatically improve wall strength without the need of filling all cells with concrete.
3. Wall integrity- Wind resistant roof attachment without costly custom roof tie-down straps due to metal truss fasteners embedded into the bond-beam concrete.
4. Self standing – CMUs self stand seven courses high without incident. I mortar the 7th course to the 6th course (bottom mortar only) to re-establish a level and plumb wall. This also establishes a firm base for the top half of the wall. Above the 7th course, I stair-step-stack the corners all the way to the top and use the corner to brace itself.
5. Local availability – CMUs are available just about everywhere. If you need more, just go get some more. Not so with those custom blocks.
6. Design engineering – Custom blocks always require costly design engineering, whereas CMU construction falls under the building code empirical design standards and requires no specific engineering studies. Just obey the empirical design block home construction requirements of your local building authority.
7. Special glues – CMU requires no special or expensive bonding agent to stack the blocks. Normal mortar is used to set the first course on the foundation/slab. The cost of the SBC is offset because it costs less than conventional house siding materials.